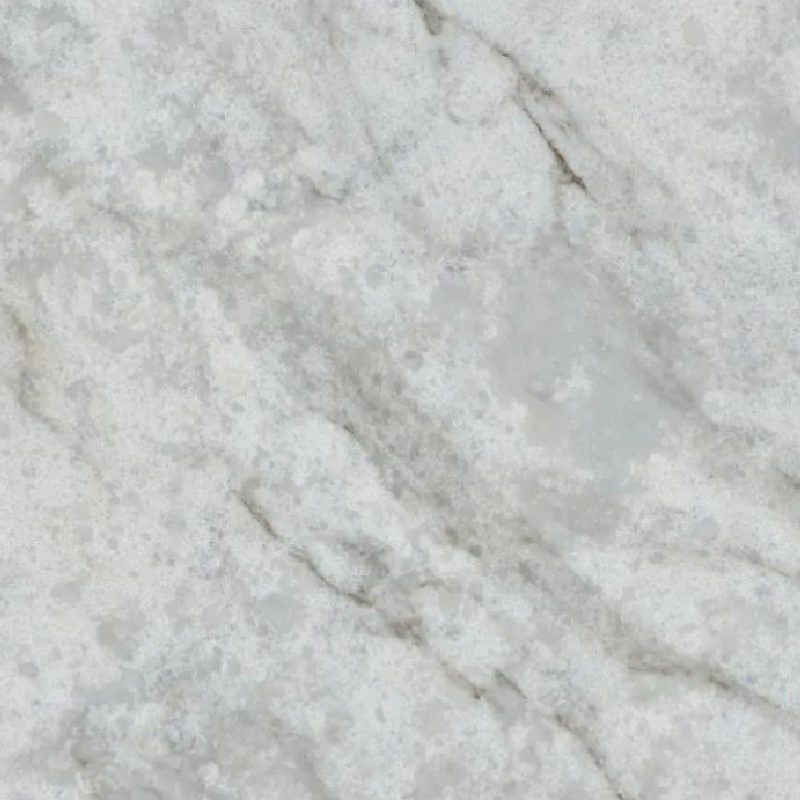
Abstract
This article delves into the pivotal role of unsaturated polyester resin in artificial stone production. It comprehensively analyzes the existing challenges in the process, such as high resin costs, potential environmental pollution, and quality instability. Through in - depth exploration of process optimization measures, including raw material selection, formulation adjustment, and process parameter control, as well as quality control methods like strict inspection at each production stage and the establishment of a comprehensive quality management system, it aims to enhance the overall quality of artificial stone products. Additionally, it introduces Fangxin Resin, highlighting its outstanding performance and reliability in artificial stone production, providing new ideas and options for the industry.
1. Introduction
Artificial stone, with its unique advantages such as rich colors, high strength, and easy processing, has witnessed a surging demand in the construction and decoration markets in recent years. As a crucial binder in artificial stone production, unsaturated polyester resin significantly impacts the product's quality, performance, and cost. Optimizing the process of using unsaturated polyester resin and effectively controlling quality are not only essential for improving product competitiveness but also crucial for promoting the sustainable development of the artificial stone industry.
2. Role of Unsaturated Polyester Resin in Artificial Stone
2.1 Bonding Function
Unsaturated polyester resin serves as the "glue" that binds various inorganic fillers, such as quartz sand and calcium carbonate, together in artificial stone. It forms a continuous phase in the composite material, ensuring that the fillers are firmly adhered to each other, endowing the artificial stone with sufficient strength and integrity. For example, in the production of quartz - based artificial stone, the unsaturated polyester resin infiltrates between the quartz particles, and after curing, it creates a strong bond, enabling the stone to withstand various mechanical forces during use.
2.2 Influence on Physical and Chemical Properties
The type and amount of unsaturated polyester resin can directly affect the physical and chemical properties of artificial stone. A high - quality resin can improve the hardness, wear - resistance, and corrosion - resistance of artificial stone. For instance, resins with appropriate cross - linking density can enhance the hardness of artificial stone, making it more suitable for applications in high - traffic areas like kitchen countertops. Moreover, the chemical structure of the resin can also influence the artificial stone's resistance to acids, alkalis, and solvents, expanding its application scenarios.
3. Current Challenges in the Process
3.1 High Resin Cost
Unsaturated polyester resin often constitutes a significant portion of the production cost in artificial stone manufacturing. The complex synthesis process of the resin and the relatively high price of raw materials contribute to this high cost. As a result, manufacturers are constantly seeking ways to reduce resin usage without sacrificing product quality. Some attempts to use low - cost resins have led to a decline in product performance, such as reduced strength and poor durability.
3.2 Environmental Pollution Concerns
During the production and curing of unsaturated polyester resin, volatile organic compounds (VOCs) may be released, posing potential risks to the environment and human health. Additionally, the disposal of waste resin and artificial stone products at the end - of - life stage also raises environmental challenges. The non - biodegradable nature of traditional unsaturated polyester resins makes their disposal difficult, and improper disposal can lead to soil and water pollution.
3.3 Quality Instability
The quality of artificial stone products is highly dependent on the quality of the unsaturated polyester resin and the production process. Fluctuations in resin quality, such as inconsistent molecular weight and cross - linking degree, can result in inconsistent product quality. In addition, improper process control, such as inaccurate mixing ratios of resin and fillers, and inconsistent curing conditions, can also lead to problems such as internal voids, cracks, and uneven color in artificial stone products.
4. Process Optimization Measures
4.1 Raw Material Selection
4.1.1 Choosing High - Quality Resin
Selecting high - quality unsaturated polyester resin is the foundation of ensuring product quality. High - quality resins typically have more stable chemical properties, uniform molecular weight distribution, and better reactivity. For example, resins with a narrow molecular weight distribution can ensure more consistent cross - linking during the curing process, resulting in products with more stable physical properties. When choosing a resin supplier, manufacturers should consider factors such as the supplier's reputation, production technology, and product quality testing reports. Fangxin Resin, for example, has a well - established reputation for producing high - quality unsaturated polyester resins. Their advanced production technology and strict quality control system ensure that each batch of resin has consistent quality, providing a reliable guarantee for artificial stone manufacturers.
4.1.2 Optimizing Filler Selection
In addition to resin, the selection of fillers also has a significant impact on the performance and cost of artificial stone. Different fillers have different particle sizes, shapes, and surface properties, which can affect the workability of the resin - filler mixture and the final properties of the artificial stone. For example, using fillers with a proper particle size distribution can reduce the amount of resin required while maintaining good mechanical properties. Fine - grained fillers can fill the voids between coarser particles, forming a more compact structure. Moreover, surface - treated fillers can improve their compatibility with the resin, enhancing the interfacial bonding strength and overall performance of the artificial stone.
4.2 Formulation Adjustment
4.2.1 Reducing Resin Content
To address the issue of high resin costs, researchers and manufacturers have been exploring ways to reduce the amount of resin used in artificial stone production. One effective method is to optimize the formulation by using additives or modifying the fillers. For example, adding certain types of nanoparticles can improve the mechanical properties of the composite material, allowing for a reduction in resin content. Some studies have shown that adding a small amount of nanoclay to the resin - filler system can enhance the tensile and flexural strength of artificial stone, enabling a 10% - 20% reduction in resin usage. Another approach is to use fillers with low oil absorption values, as less resin is required to wet these fillers.
4.2.2 Adding Additives
Adding appropriate additives can improve the performance of unsaturated polyester resin and artificial stone products. For example, antioxidants can prevent the resin from aging and degrading during processing and use, extending the service life of the artificial stone. UV absorbers can enhance the product's resistance to ultraviolet rays, preventing color fading. Flame retardants can be added to make the artificial stone fire - resistant, expanding its application in areas with fire - safety requirements. Additionally, plasticizers can be used to improve the flexibility of the resin, reducing the brittleness of the artificial stone and making it more suitable for some special applications.
4.3 Process Parameter Control
4.3.1 Mixing Process
The mixing process is crucial for ensuring the uniform distribution of resin and fillers. Appropriate mixing speed, time, and order can significantly affect the quality of the artificial stone. If the mixing speed is too low, the resin and fillers may not be evenly distributed, resulting in local defects in the product. On the other hand, if the mixing speed is too high, it may cause excessive shear force, damaging the structure of the resin and fillers. The mixing time should also be carefully controlled to ensure that the resin fully wets the fillers. In addition, the order of adding components can also impact the mixing effect. For example, adding fillers gradually to the resin while stirring can promote better wetting and dispersion.
4.3.2 Curing Process
The curing process of unsaturated polyester resin determines the final properties of the artificial stone. Controlling factors such as curing temperature, curing time, and the amount of curing agent is essential. Different resins have different optimal curing conditions. For example, some resins may require a higher curing temperature to achieve complete cross - linking, while others may be more sensitive to curing time. If the curing temperature is too low or the curing time is too short, the resin may not cure completely, resulting in products with low strength and poor durability. Conversely, if the curing temperature is too high or the curing time is too long, the product may become over - cured, leading to brittleness and cracking.
5. Quality Control Methods
5.1 Raw Material Inspection
Strict inspection of raw materials, including unsaturated polyester resin and fillers, is the first step in quality control. For resin, parameters such as viscosity, acid value, and gel time should be tested to ensure that they meet the production requirements. The quality of fillers, such as particle size distribution, moisture content, and purity, should also be carefully inspected. Any deviation in raw material quality can have a significant impact on the final product quality. For example, if the moisture content in the filler is too high, it can react with the resin during the curing process, causing bubbles and reducing the strength of the artificial stone.
5.2 In - Process Quality Monitoring
During the production process, continuous quality monitoring is necessary. This includes monitoring the mixing process to ensure uniform distribution, and checking the appearance and properties of the semi - finished products at various stages. For example, in the molding stage, the thickness and flatness of the artificial stone blanks should be measured to ensure they meet the standards. In addition, non - destructive testing methods, such as ultrasonic testing, can be used to detect internal defects in the semi - finished products, allowing for timely adjustment of the production process.
5.3 Final Product Testing
After the artificial stone products are produced, comprehensive final product testing should be carried out. This includes testing of mechanical properties such as hardness, tensile strength, and flexural strength, as well as testing of chemical properties such as corrosion resistance and heat resistance. Appearance inspection, including color uniformity, surface smoothness, and the presence of defects, is also an important part of final product testing. Only products that pass all the tests can be released to the market, ensuring that consumers receive high - quality artificial stone products.
6. Introduction to Fangxin Resin
Fangxin Resin has emerged as a leading player in the field of unsaturated polyester resin production, especially for artificial stone applications. Their products are characterized by high purity, stable performance, and excellent compatibility with various fillers.
6.1 Product Features
6.1.1 High Cross - Linking Density
Fangxin Resin's products are designed to achieve a high cross - linking density after curing. This results in artificial stone products with excellent hardness and wear - resistance. The high cross - linking density also enhances the chemical stability of the resin, making the artificial stone more resistant to environmental factors such as moisture and chemical substances.
6.1.2 Low VOC Emissions
In response to environmental concerns, Fangxin Resin has made significant efforts to reduce VOC emissions in its products. Their advanced production technology and formula optimization have enabled the development of resins with low VOC content, which not only meet environmental protection requirements but also contribute to a healthier indoor environment when used in artificial stone for interior decoration.
6.2 Application Cases
Many artificial stone manufacturers have successfully applied Fangxin Resin in their production processes and achieved remarkable results. For example, a well - known artificial stone company reported that after switching to Fangxin Resin, the quality of their products became more stable. The rate of product defects decreased significantly, and the mechanical properties of the artificial stone, such as flexural strength and impact resistance, were improved by 15% - 20%. In addition, the low VOC emissions of Fangxin Resin also helped the company meet the strict environmental standards of some high - end markets, expanding their market share.
7. Conclusion
In conclusion, the process optimization and quality control of unsaturated polyester resin in artificial stone production are of great significance for the development of the artificial stone industry. By addressing current challenges through measures such as raw material selection, formulation adjustment, process parameter control, and strict quality control, manufacturers can improve the quality and performance of artificial stone products while reducing costs and environmental impacts. The introduction of high - quality resins like Fangxin Resin provides new impetus for the industry's development. As technology continues to advance, it is expected that more innovative solutions will emerge in the future, further promoting the growth and sustainability of the artificial stone industry.